PRODUCTION PROCESS

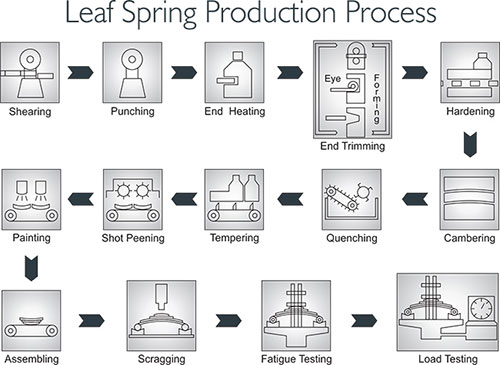
Lamina introduces INDIA’S FIRST ROBOT CONTROLLED HEAT LINE IN LEAF SPRING INDUSTRY
VIDEO
Advantages are as follows:
- Consistent quality springs in terms of even hardness and shape.
- No cold working, Side bend removal after Heat Treatment.
- Many references can be done at the same time since there are 6 stations.
- No manual intervention because of the Robot’s, so every leaf is quenched with least amount of time in air and hence consistent hardness.
- Huge quantity of quench oil of about 95,000 litres and a powerful cooling system would ensure that the temperature of oil bath is maintained at 60-65 Degree centigrade.
- LPG Fired furnaces with the automatic control of the different zones in furnaces to ensure good surface finish without any overheating of the leaves.
- Heavy Duty column type quenching station with 3 cylinders ensures cambering all kinds of leafs especially thicker parabolic leaves with Centre Flatness.
- Quenching Station (Heavy Duty - 3 Nos) with swing would ensure proper agitation of the quench oil and would ensure uniform hardness in the entire leaf (same hardness in the centre as will in the ends.)
- Water Shower after tempering is also used to further toughen the Heat Treated Leaf.
- Four impeller fully automatic High Stress Shot Peening machine, to ensure that all the parabolic springs are stress peened, which substantially increases the life of the parabolic spring.
- Induction End Heating Machine to ensure optimal heating of the spring for End processes and avoid overheating of the leaves.
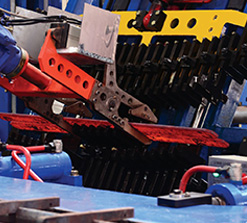
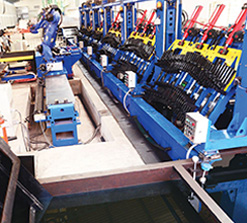
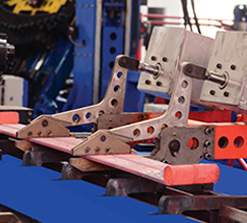
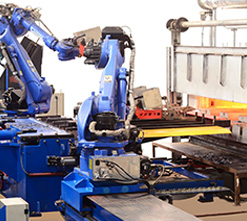